Custom built by JB Aircraft Engines in Sebring, Florida.
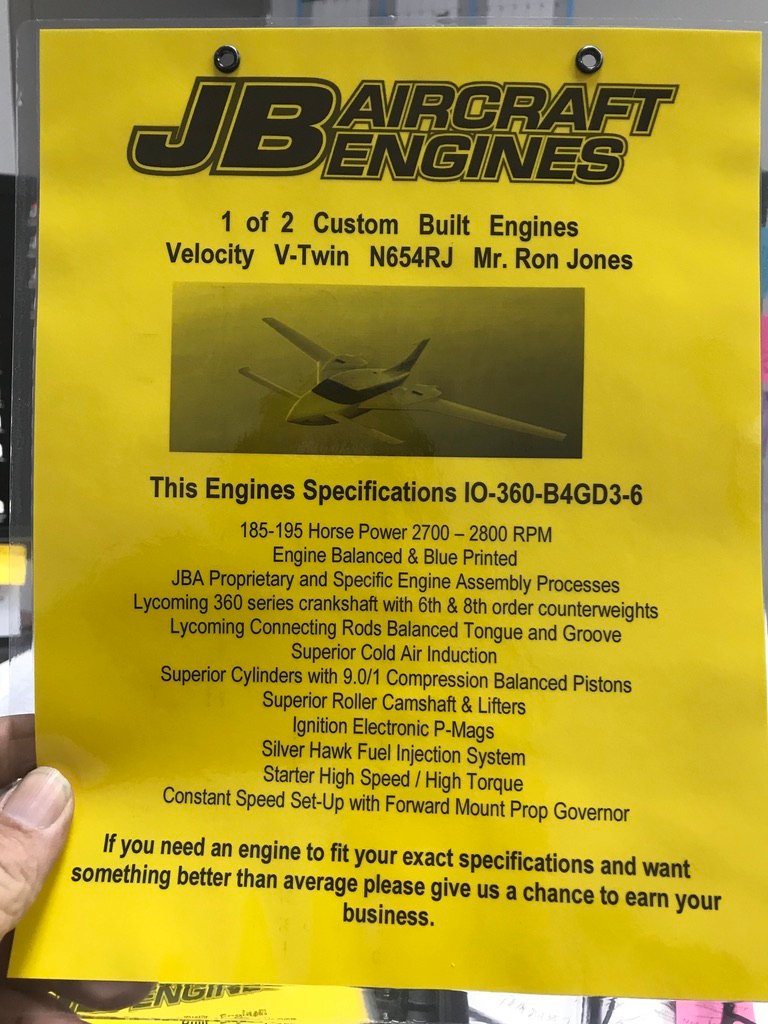
Based on my experience with previous airplanes, including two twin engine models, I knew that I wanted to ensure the engines would run as smoothly as possible (for a reciprocating engine). So I specified a number of options toward this end.
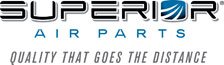
First, I opted for the Lycoming counterbalanced crankshaft. While I do prefer the Superior engines for a lot of reasons, things like roller cams, the ability to replace the lifters without splitting the case, and so on, I decided on Lycoming counterbalanced crankshafts to enhance smooth running. Like anything, this option has pluses and minuses. For example, since you can’t “horse” the throttle around (no abrupt movements), I wouldn’t recommend this for an acrobatic airplane like a RV-8. But for a twin, there is really no need to make quick, abrupt throttle changes. That caveat is worth it in order to have a smoother running engine.
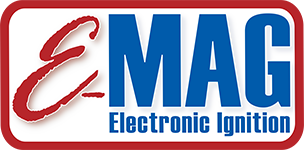
Second, I opted to go with all PMag electronic ignitions, as in two on each engine. No magnetos. This results in slightly better fuel economy as the timing will be advanced for cruise. It also makes for a smooth idle and easier starting, especially on hot starts.
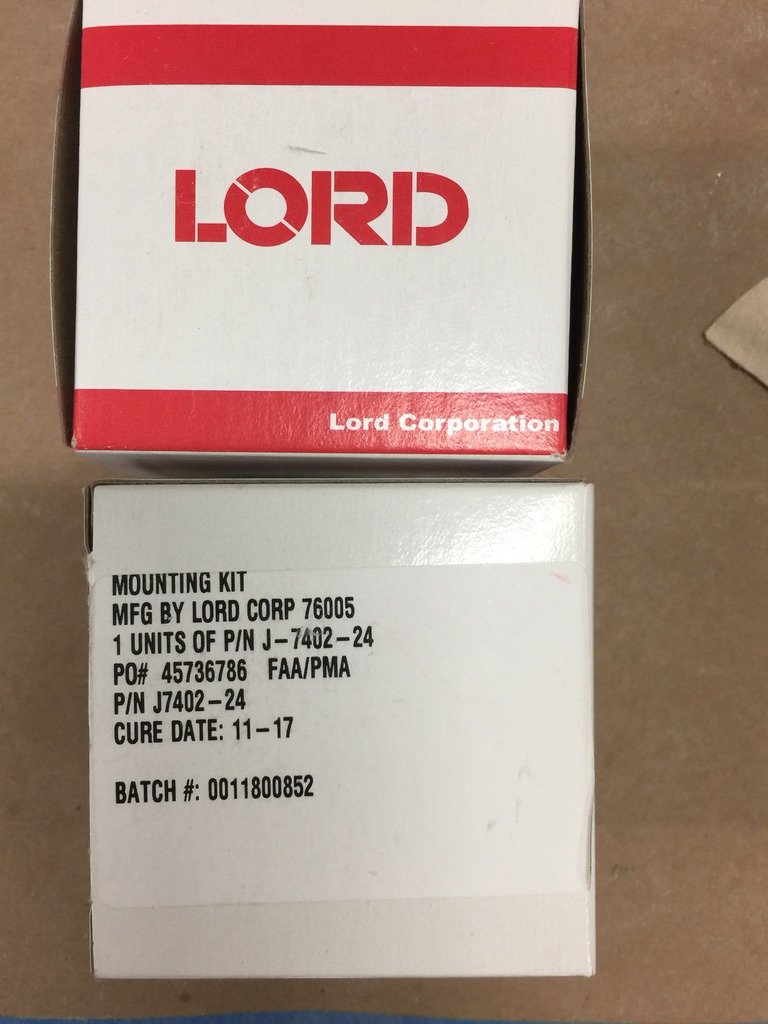
Third, I opted for Lord engine mounts. They are somewhat softer than Barry engine mounts, and they cost just a little more. But the engine vibration that is transferred to the air-frame is definitely less with these isolators. I got mine at Aircraft Spruce. The only downside is they might not last quite as long, maybe only a 1,000 hours or so until they will need replacing. I’d rather have the smoother engines.